Dossier
Recent endeavours showcasing our expertise and successful track record in delivering innovative and impactful solutions in various fields.
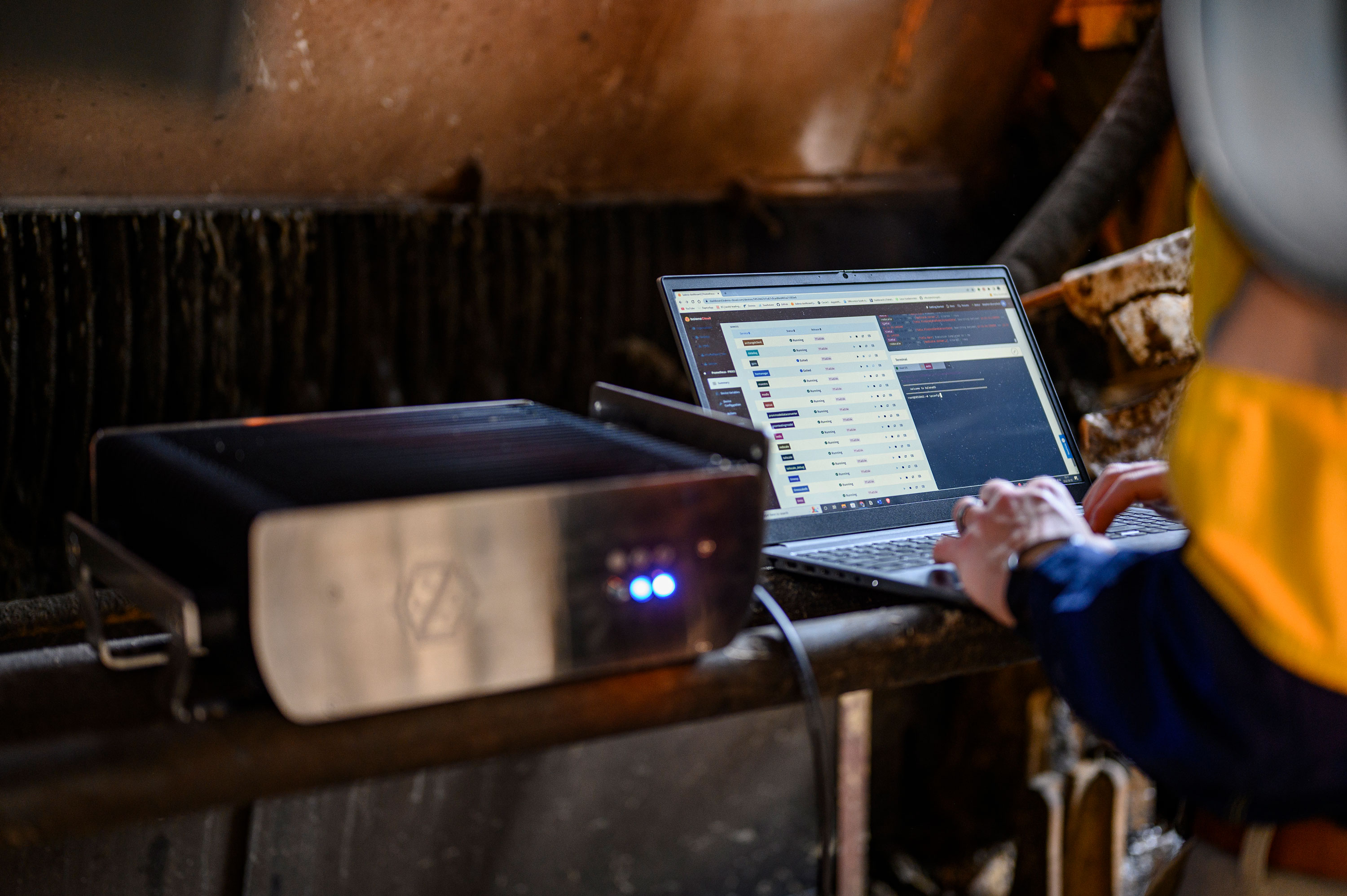
Maintaining the Cutting Edge
Nanodyn envisages a synergy of centralised Cloud and federated Edge computing, to provide truly effective, system-wide optimisation.
Innovation Velocity
Keep posted on recent endeavours and innovative and impactful solutions in various fields.
Refinery Filter Scheduler
Filtration is a crucial step in many industrial processes. The Refinery Filter Scheduler (RFS) is an advanced process control scheduling algorithm for the optimisation of filter cleaning. The RFS predicts the fouled state and efficiency of a number of filters to create an optimal cleaning schedule.
This optimises flow through the filter bank and thereby maximises production throughput. The RFS was successfully implemented in the Refinery at Malalane Sugar Mill, South Africa, where the model performance was tracked and validated over 25 days.
On average, flow through the refinery’s 8 filters increased after adoption of the scheduler. Given sufficient feed supply, adoption of the RFS at Malalane Mill increased the daily production of refined sugar by 308 tonnes. This equates to a more than 25% increase in daily production when compared to historical refinery performance over the course of the three production seasons.
Following adoption of the RFS, the Malalane Mill broke its refined sugar production record twice within 48 hours.
Presentation of these results at the South African Sugar Technologists’ Association’s annual congress was awarded the coveted Cecil-Renaud Factory Prize for the best paper by authors not part of a scientific or technological institute.
Download the PaperThis optimises flow through the filter bank and thereby maximises production throughput. The RFS was successfully implemented in the Refinery at Malalane Sugar Mill, South Africa, where the model performance was tracked and validated over 25 days.
On average, flow through the refinery’s 8 filters increased after adoption of the scheduler. Given sufficient feed supply, adoption of the RFS at Malalane Mill increased the daily production of refined sugar by 308 tonnes. This equates to a more than 25% increase in daily production when compared to historical refinery performance over the course of the three production seasons.
Following adoption of the RFS, the Malalane Mill broke its refined sugar production record twice within 48 hours.
Presentation of these results at the South African Sugar Technologists’ Association’s annual congress was awarded the coveted Cecil-Renaud Factory Prize for the best paper by authors not part of a scientific or technological institute.
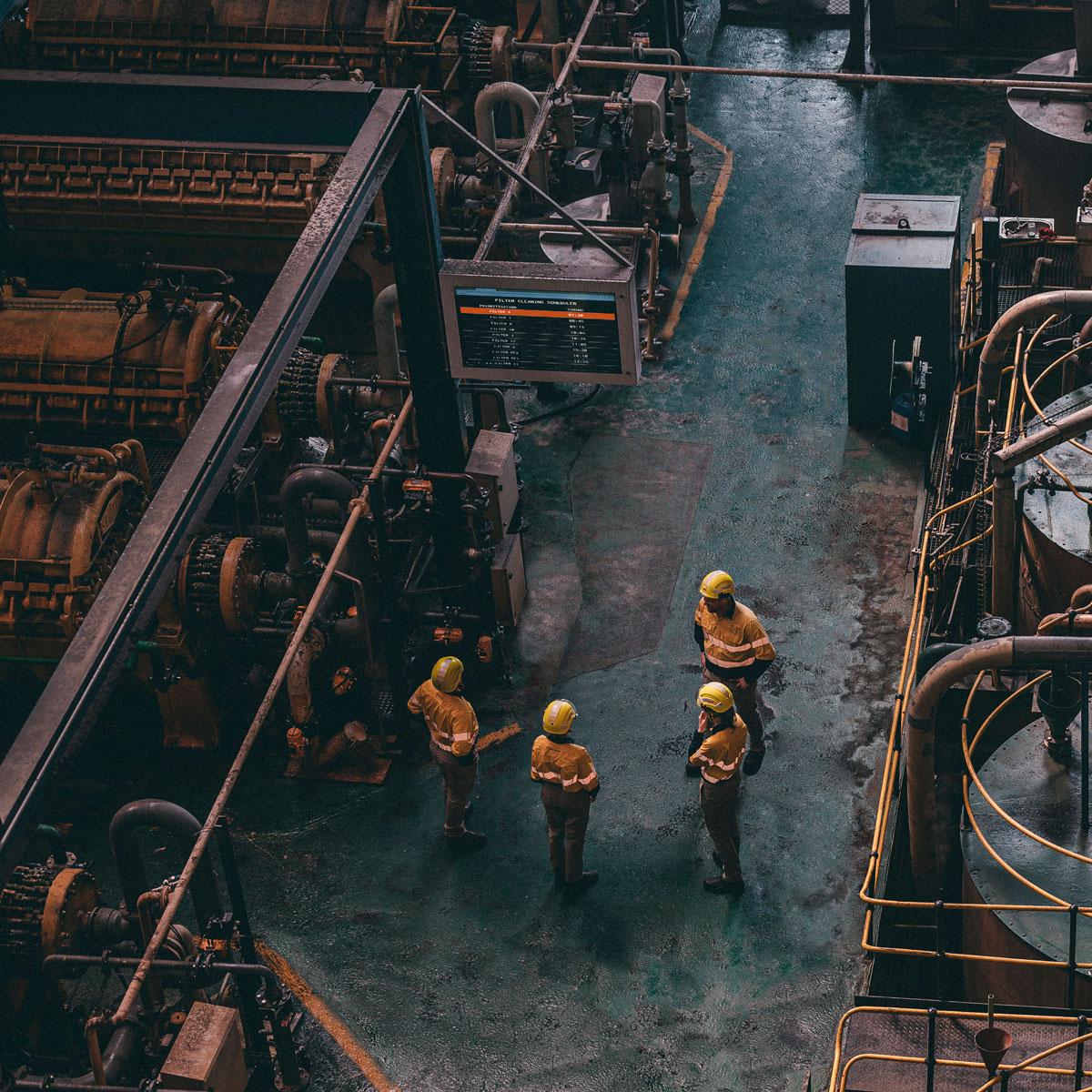
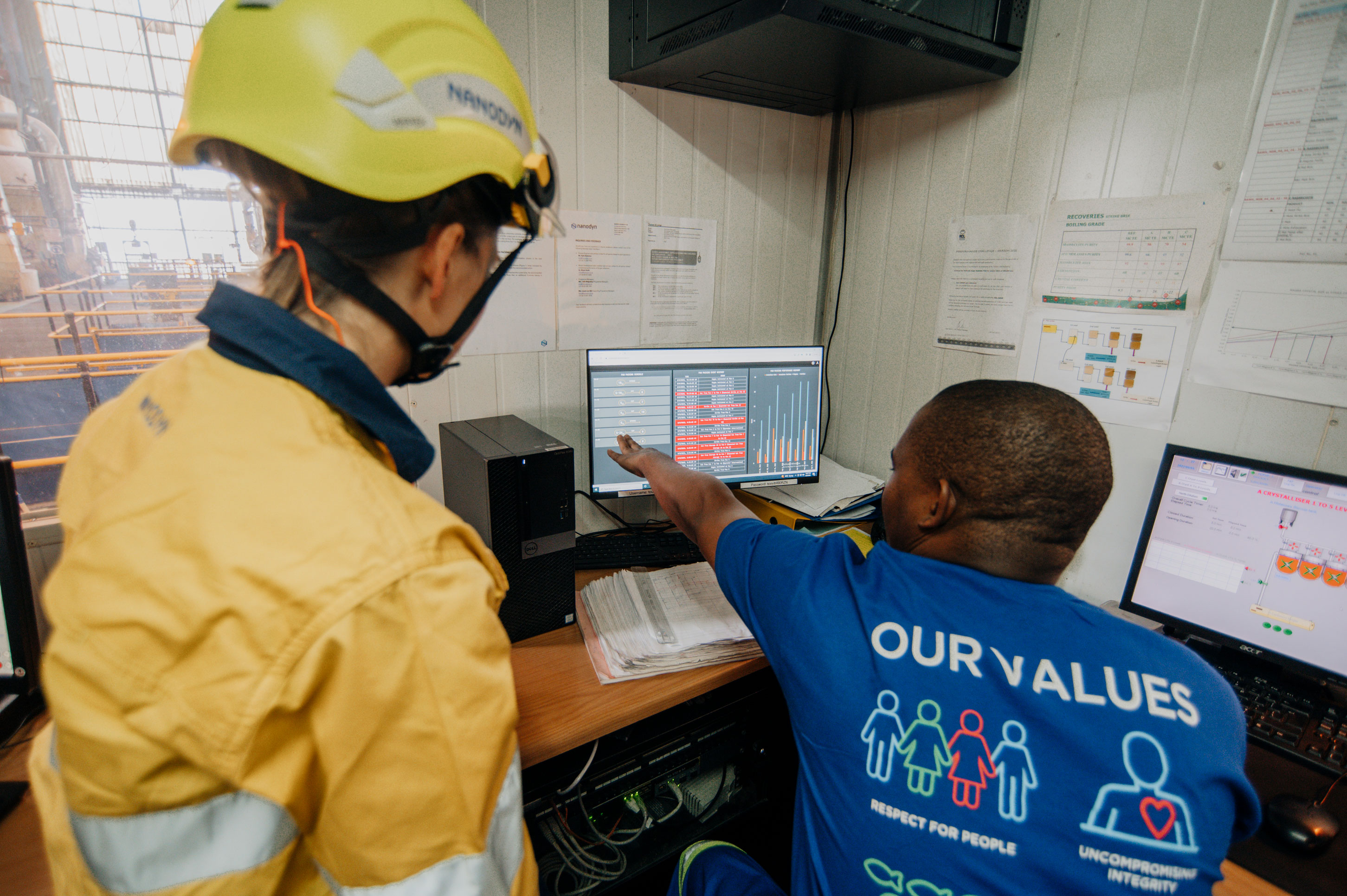
A-Pan Scheduler
During sugar production, sugar is transferred in batches between a series of crystallisation pans, following a complex non-linear pathway. The A-Pan Scheduler is a scheduling algorithm that optimises a set of these pans, the A-pans, by considering possible future events in the pan packing process.
By reducing scheduling conflicts and the need for operator improvisation, pan throughput can be increased, while energy consumption is decreased.
The A-Pan Scheduler was specifically designed for the Malalane Sugar Mill in South Africa. It was implemented and validated over a period of 1 month. Upon adoption an increase in batch completions was observed (a higher strike rate), along with a higher production consistency amid plant irregularities, leading to a more predictable factory output
By reducing scheduling conflicts and the need for operator improvisation, pan throughput can be increased, while energy consumption is decreased.
The A-Pan Scheduler was specifically designed for the Malalane Sugar Mill in South Africa. It was implemented and validated over a period of 1 month. Upon adoption an increase in batch completions was observed (a higher strike rate), along with a higher production consistency amid plant irregularities, leading to a more predictable factory output
Trailblazing The Advanced Process Control Trajectory
The full information cycle capability that drives actionable intelligence in what is traditionally termed - "Closed Loop" Control.
Utilising Archangel, Nanodyn’s proprietary digital architecture, industrial process conditions are continuously monitored, data is captured and data is transmitted as input to control algorithms running in the cloud and output as real or near real-time action.
In this proof-of-concept demonstration, an industrial flow control valve is remotely instructed to change position based on a predicted expected upstream flow model while minimising rapid downstream tank level fluctuations in order to maintain a stable and orderly operation. Furthermore, when disruptive conditions are predicted by the algorithm, it sends preventative actions to be performed to minimise any negative impact.Behold the technology for ‘no-human-in-the-loop’, reactive, Advanced Process Control.
Utilising Archangel, Nanodyn’s proprietary digital architecture, industrial process conditions are continuously monitored, data is captured and data is transmitted as input to control algorithms running in the cloud and output as real or near real-time action.
In this proof-of-concept demonstration, an industrial flow control valve is remotely instructed to change position based on a predicted expected upstream flow model while minimising rapid downstream tank level fluctuations in order to maintain a stable and orderly operation. Furthermore, when disruptive conditions are predicted by the algorithm, it sends preventative actions to be performed to minimise any negative impact.Behold the technology for ‘no-human-in-the-loop’, reactive, Advanced Process Control.